Виды ремонта и общая схема технологического процесса
Для систем и агрегатов танкового электрооборудования, как и для агрегатов силовой установки и силовой передачи танка, принято различать два вида ремонта: капитальный и текущий.
Капитальный ремонт электрооборудования и танковых автоматических систем осуществляется при капитальном ремонте танков. Схема технологического процесса капитального ремонта включает в себя следующие основные этапы: демонтаж системы с объекта, полную разборку всех агрегатов и узлов, дефектацию всех деталей, ремонт или замену неисправных деталей и узлов, сборку и испытание агрегатов, монтаж системы на объекте и ее испытание. По указанной схеме могут ремонтироваться все системы электрооборудования и автоматики бронетанковой техники вне зависимости от характера их использования за межремонтный пробег объекта.
По характеру использования за межремонтный пробег машины системы электрооборудования и автоматики можно разбить на две большие группы.
К первой группе следует отнести системы, наработка которых полностью определяется пробегом машины до капитального ремонта. Агрегаты этих систем к сроку выхода объекта в капитальный ремонт в большинстве случаев полностью вырабатывают свой межремонтный ресурс. В эту группу входят системы и агрегаты, работающие совместно с двигателем или обеспечивающие его работу, например, зарядная цепь, системы контроля режима двигателя.
Достаточно многочисленной является вторая группа систем, наработка которых не всегда соответствует пробегу машины. Сюда входят приборы ночного видения, стабилизаторы и другие системы. Наработка этих систем зависит от вида боевой подготовки, на котором преимущественно использовалась машина. Такие системы, как стабилизаторы, могут за межремонтный пробег объекта не отработать своего гарантийного срока. А узлы некоторых систем могут включаться только для их проверки.
На рис. 255 изображено рассеивание наработок стабилизаторов по пробегам машин. Из графика видно, что для отдельно взятых танков наблюдается естественная функциональная зависимость между пробегами машины и наработкой стабилизаторов. В первом приближении в отдельные периоды эксплуатации зависимость эта линейна и может быть описана обычным уравнением прямой вида t = АS + В, где t— время работы стабилизатора, ч; S—пробег машины, км; А и В — коэффициенты, являющиеся случайными величинами. Поэтому в целом для большого количества танков наработка стабилизаторов не может быть определена пробегом однозначно.
На рис. 256 представлены графики распределения вероятностей наработок стабилизаторов до капитального ремонта танков в условиях мирного времени. Из этих графиков следует, что от 50 до 95%
стабилизаторов различных объектов бронетанковой техники за межремонтный пробег не успевают вырабатывать гарантийный срок службы.
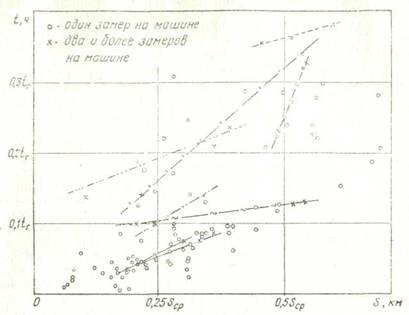
Рис. 255. Рассеивание наработок стабилизаторов по пробегам танков
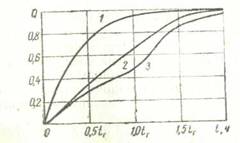
Рис. 256. Распределение вероятностей наработок стабилизаторов до капитального ремонта машин:
1 и 2 — для средних танков; 3 — для легкого танка
Вид и объем ремонта любого агрегата, системы или машины должны находиться в строгом соответствии с техническим состоянием объекта ремонта. Однако техническое состояние агрегатов и
узлов систем электрооборудования и автоматики, в отличие от агрегатов силовой установки и силовой передачи, определяется не только наработкой, т. е. израсходованным ресурсом, но и календарными сроками службы. При малой наработке, но значительном сроке службы (календарном времени с момента изготовления или капитального ремонта) техническое состояние агрегатов электрооборудования будет определяться не величинами износов, а изменениями физических свойств изоляции и уплотнений за счет естественного старения изоляционных и уплотняющих материалов.
Капитальный ремонт танка должен, с одной стороны, обеспечить надежную работу всех его систем в течение очередного межремонтного срока, а с другой — должен проводиться в минимальные сроки и быть достаточно экономичным. Поэтому для агрегатов систем, имеющих малую наработку, иногда целесообразно провести углубленную оценку технического состояния и текущий ремонт профилактического характера. При углубленной оценке технического состояния особое внимание должно быть обращено на проверку качества изоляции и уплотнений. В схему технологического процесса ремонта агрегатов в этом случае должны войти следующие этапы: частичной разборки, чистки, оценки технического состояния, замены некоторых изоляционных и уплотнительных деталей, восстановления антикоррозионных покрытий, устранения неисправностей, не приводящих к потере работоспособности, и т. п.
Таким образом, вид и объем ремонта систем электрооборудования и автоматики для танков, поступивших в капитальный ремонт, должны определяться величиной наработки, сроком службы и техническим состоянием их агрегатов. В этом случае выбранный вид ремонта должен обеспечить работоспособность системы до очередного ремонта танка.
Капитальный ремонт системы заключается в капитальном ремонте (замене) или всех ее агрегатов и узлов, или основных с проведением текущего ремонта профилактического характера остальным узлам системы. В обоих случаях после капитального ремонта система испытывается по существующим техническим условиям.
Основная цель капитального ремонта агрегата — обеспечить его надежную работу до следующего планового ремонта танка, т. е. восстановить ресурс этого агрегата.
Сущность и объем выполняемых работ при капитальном ремонте агрегатов электрооборудования и автоматики те же, что и для механических агрегатов. Схема технологического процесса капитального ремонта агрегатов электрооборудования и автоматики представлена на рис. 257. Последовательность этапов одинакова при ремонте различных групп агрегатов; содержание каждого этапа различно и будет рассмотрено при изучении технологии их ремонта.
Серьезное различие имеется в характере испытаний, проводимых после капитального ремонта, например, агрегатов трансмиссии и агрегатов электрооборудования.
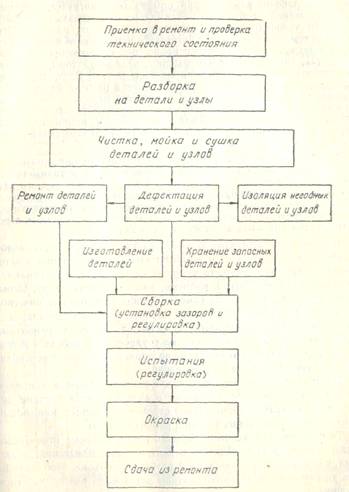
Рис 257. Схема технологического процесса капитального ремонта агрегатов электрооборудования и автоматики бронетанковой техники
Агрегаты электрооборудования в отличие от агрегатов транс-мисии после капитального ремонта испытываются не на холостом ходу, а в рабочих режимах при номинальной нагрузке. Режимы этих испытаний необходимо максимально приближать к наиболее тяжелым условиям работы агрегатов на боевых машинах. Это вызвано тем, что приложение нагрузки и изменение ее величины существенно влияют на характер процессов, протекающих в таких агрегатах, как электрические машины, реле-регуляторы, электронные усилители, гироскопические приборы и т. п. Если, например, для электрических генераторов испытания в режиме двигателя на холостом ходу позволяют судить о качестве механической сборки, то о качестве электрической сборки можно судить только на основании их испытаний в генераторном режиме при номинальной нагрузке. Поэтому оценить качество ремонта путем испытаний на холостом ходу невозможно.
Текущий ремонт систем и агрегатов электрооборудования и автоматики выполняется подвижными ремонтными средствами танковых войск в полевых условиях или в условиях стационарного размещения ремонтных подразделений и частей. Сущность текущего ремонта систем и агрегатов электрооборудования и автоматики состоит в устранении неисправностей путем замены отказавших агрегатов, узлов или вышедших из строя деталей.
В отличие от агрегатов ходовой части, трансмиссии, силовой установки и т. п. системы и агрегаты электрооборудования и автоматики в процессе текущего ремонта, как правило, испытывают в режимах, приближенных к рабочим, или на холостом ходу. Испытания проводятся в начале ремонта, чтобы проверить техническое состояние и выявить неисправный агрегат, узел или деталь, а в конце ремонта — установить качество выполнения ремонтных работ. Эта особенность обусловлена трудностью, а иногда и невозможностью визуального определения характера и места неисправности, а также полноты ее устранения.
Поскольку определяющим в видах ремонта является вопрос о восстановлении ресурса, то замена в автоматической системе какого-либо агрегата на капитально отремонтированный или новый представляет собой лишь текущий ремонт системы.
Технологический процесс текущего ремонта, кроме отмеченных выше этапов предварительного и контрольного испытаний, включает, как правило, этап частичной разборки в объеме, необходимом для устранения неисправности, этапы устранения неисправности и сборки.
Полные схемы технологических процессов для конкретных групп агрегатов будут рассмотрены в соответствующих главах раздела. 500
|